新浪军事编者:为了更好的为读者呈现多样军事内容,满足读者不同阅读需求,共同探讨国内国际战略动态,新浪军事独家推出《深度军情》版块,深度解读军事新闻背后的隐藏态势,立体呈现中国面临的复杂军事战略环境,欢迎关注。
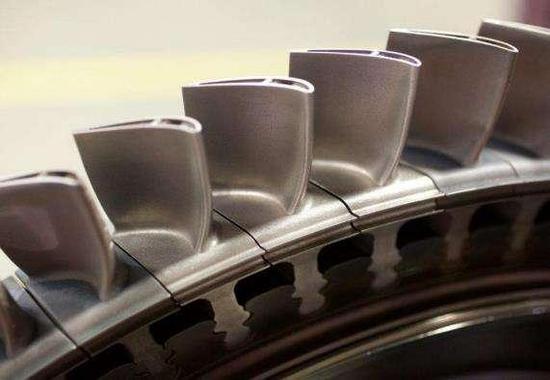
近年来3D打印技术为人们所熟悉,它又被称为“快速成型技术”或“增材制造技术”,诞生于上世纪80年代末,主要是以数字模型文件为基础,通过材料叠层添加构造三维物体的变革性、数字化增材制造技术。并逐渐成为一种新兴的制造方式,很多国家,包括美国、德国等都高度重视并积极推广应用该技术。德国西门子公司近日完成了涡轮叶片的3D打印,并将此叶片安装在发动机中进行了满负荷运转试验,由于叶片工艺复杂、加工精度要求高、制造难,价格昂贵,这次用3D打印叶片标志着3D打印制造的技术实现了又一次重大突破。
西门子此次制造的叶片是通过在CAD中分层构建模型,然后分层制作再进行组合,完成零件的制造。材料使用的是多晶镍合金的粉末,这种材料能够耐高温高压,承受旋转时产生的巨大离心力。在试验中,转速高达1.3万转/分钟,时速高达1600千米,温度超过一千度,叶片上所承受的离心力超过10吨。

在航空发动机中叶片的加工工作量约占整个加工工作量的30%一40%。发动机叶片结构复杂,叶片型面为空间列表曲面。叶片在工作中要承受复杂应力和微震动,这样对叶片材料、机械加工工艺、热处理及表面喷涂工艺都有极高的质量要求。加上航空发动机研制过程中为了满足设计要求,叶片的设计改动比较频繁,这对叶片的加工工艺和加工进度提出了特殊要求。而叶片加工的周期和质量直接影响到航空发动机的研制周期。
据西方资料使用3D打印技术生产航空发动机将有望降低50%的制造成本,并大幅缩短生产和交付时间。过去通过传统工艺研制涡轮叶片的样件需要3年的时间,而如果采用了3D打印技术则仅需短短9周,和过去相比为整个供应链节约了70%的时间。
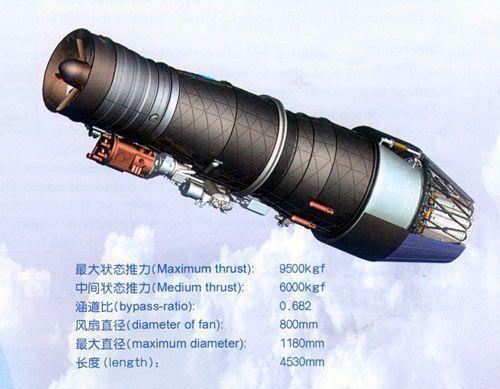
与传统工艺模式不同,3D打印技术集概念设计、技术验证与生产制造于一体。这必将极大缩小航空产品从“概念”到“定形”的时间差,从而加快航空产品的更新周期。传统的航空产品生产中,很多产品通过切割、机械加工等工序,除去多余部分形成零部件,然后被拼装、焊接成产品。这一过程中,将有90%的原材料被浪费掉;与传统工艺不同3D打印技术的航空产品的生产过程中,可直接根据计算机图形数据通过层层增加材料的方法“打印”出航空产品,按需取材,整个生产过程几乎没有浪费。

据了解,深圳某科技有限公司已经将高精度光固化3D打印技术应用到复杂空心叶片铸型的制造工艺中,可控制数百万紫外光束同时成型,并保证成型精度达20微米级别,有望为发动机定向/单晶叶片生产用陶瓷铸型一体化成型提供创新之路。现在我国在航空发动机叶片制造技术领域既面临着难得的机遇,也承受着巨大的挑战。而将金属3D打印技术引入航空发动机零部件制造领域,可响应快速制造需求,对提升我国发动机设计与制造能力具有重要意义,有望解决战机心脏病这一老大难问题。(作者署名:鼎盛军事)
本栏目所有文章目的在于传递更多信息,并不代表本网赞同其观点和对其真实性负责。凡本网注明版权所有的作品,版权均属于新浪网,凡署名作者的,版权则属原作者或出版人所有,未经本网或作者授权不得转载、摘编或利用其它方式使用上述作品。
新浪军事:最多军迷首选的军事门户!